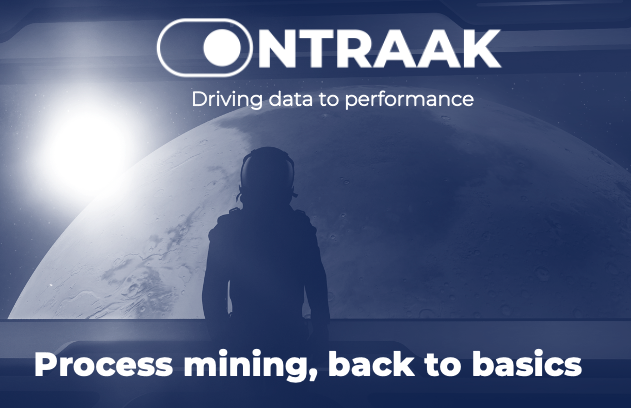
In a previous article, we talked about process mining as a powerfull solution that would finally allow us to take a step forward in the search for operational excellence and the optimisation of business processes.
Before a series of more precise, even technical articles, we share here the basics of process mining, its fundamentals and some frequent use cases.
How does process mining work?
Basically, process mining is quite simple: it is about integrating exhaustive process data in order to visualise and analyse them.
It doesn’t matter which process is involved, as long as it’s executed through the company’s information system and a “digital footprint” is generated; generally corresponding to event logs.
These allow the “life” of the process to be reconstructed, i.e. the different stages and statuses through which each element of the process has passed.
Once this data has been integrated, process mining tools are able to reconstruct, visualise and analyse the processes as they really happen.
In this way, precise insights can be found in order to elaborate relevant improvement measures (automation, user training, process reengineering, …).
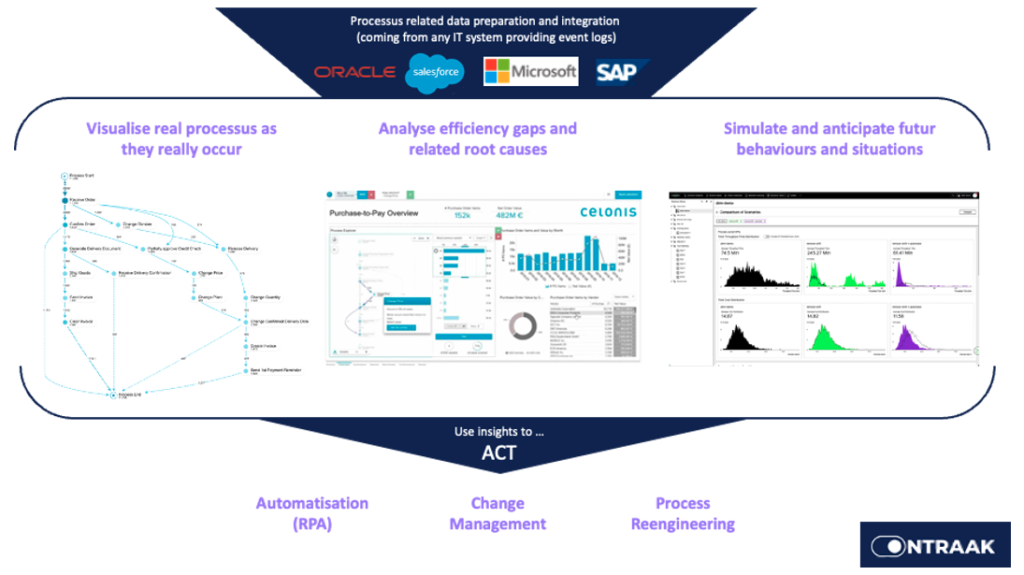
What data is required ?
In order to carry out a process analysis, the information required revolves around “event data”.
This corresponds to the data that each element (invoice, customer order, etc.) “generates” as it passes through the information system.
In concrete terms, it is made up of 3 essential pieces of information:
- A unique identifier for the object to be tracked, enabling the element to be identified from start to finish (an invoice number, an order number,…)
- The stages or steps through which this object has passed (issue of the invoice, payment made, etc.)
- The precise timestamp of the stage for the object concerned.
Other information complementary to the object to be followed can be included to refine the analysis capacity (for example the supplier concerned, the product, the quantity, the price…).
An example is better than 1000 words
Let’s take a simplified example of a sales order process (also called O2C or Order to Cash). Ideally, this process consists of 4 mains steps:
- Receipt of the customer order
- Shipment of goods
- Sending the invoice
- Receipt of payment
Let’s take a look at the digital traces generated by our order-taking system and the graphic representation of the process.
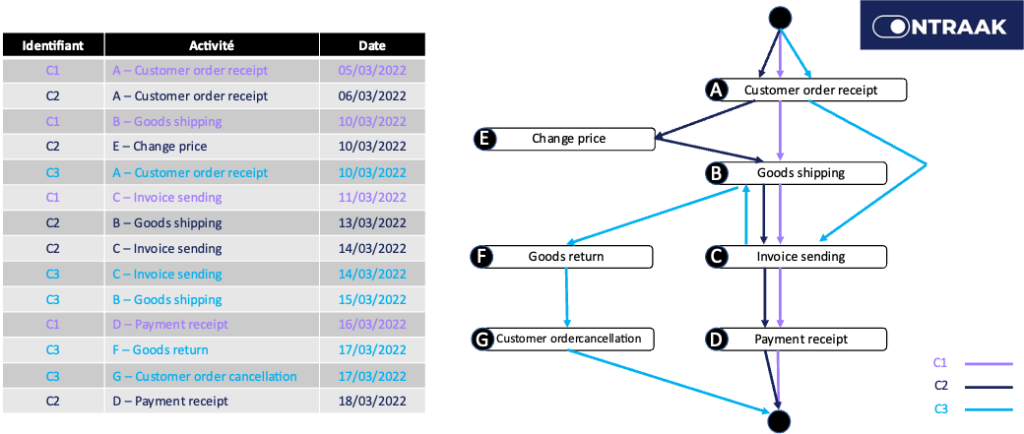
What do we quickly see? The C1 order follows the “optimal” path in contrast to C2 and C3 where we clearly see deviations, namely :
- C2 has an additional activity “Price change”.
- C3, in addition to not following the standard path (i.e. sending the goods before issuing the invoice), ends with a cancellation of the order due to a return of the goods.
Simple and straightforward, isn’t it?
Obviously, this simplistic example takes shortcuts and does not show all the analysis possibilities offered by process mining.
However, it allows us to understand the basics and to project ourselves into its concrete usage.
The potential use cases
The process analysis made possible by process mining is a real accelerator in many cases of use. Here are some examples:
- Process improvement: this is the most widespread usage. The aim here is to understand processes and their variations in order to detect opportunities for improvement and optimisation (leading to automation or process reengineering, for example).
- Process monitoring and steering: process mining solutions go beyond analysis to provide real-time steering of processes, in particular with the help of process performance KPIs (called “Process KPI Reporting”).
- Audit and compliance: process analysis enables the improvement and monitoring of process compliance with the rules and regulations in force (for example, banking regulations such as KYC or respect of internal standards’ processes).
- Process documentation: thanks to its exhaustive representation and analysis, process mining makes it much easier to document processes, with little or no updating costs.
Of course, these few use cases are not exhaustive. However, they help to materialise the usefulness and the power of process mining for all companies, small or large.
In fact, the next articles will describe how, in concrete terms, process mining is used by companies in a wide range of sectors.
In the meantime, contact us to see together how process mining can positively impact your company.